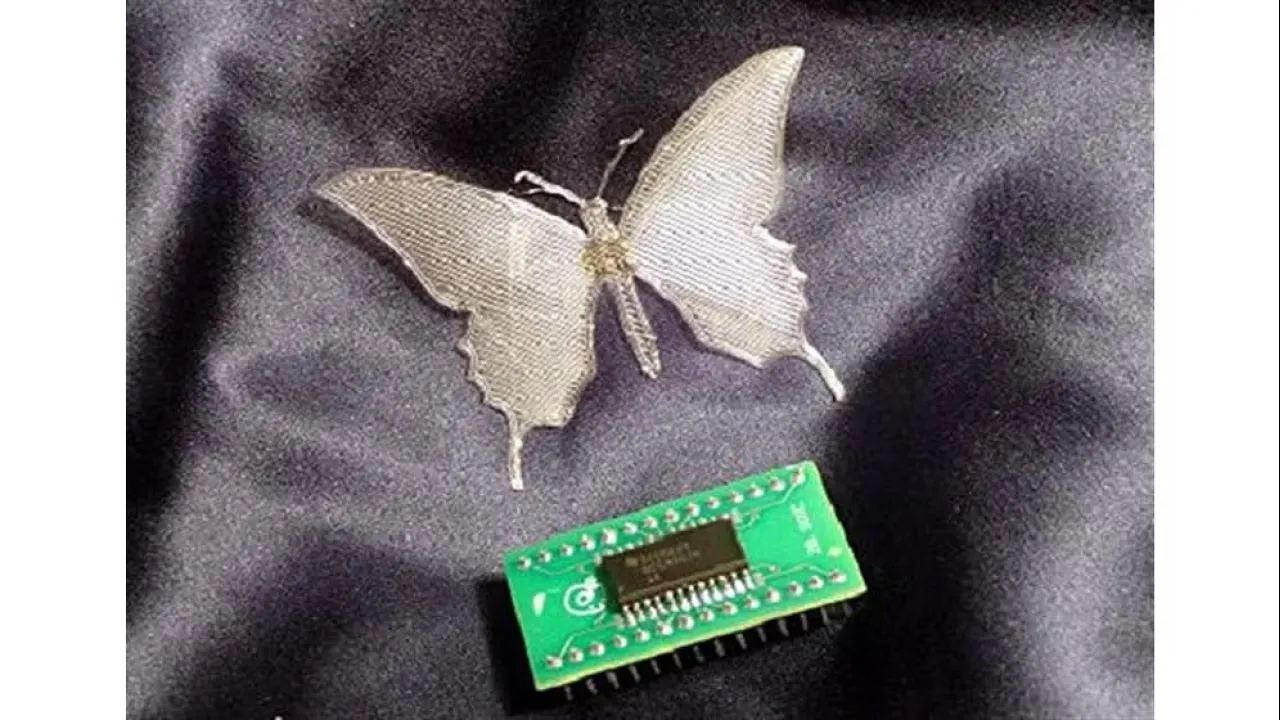
Costless and reliable 3D high-speed printing process to revolutionize decal sensors fabrication
Attempts for 3D fabrication of decal electronics were previously made. But, rigid, bulky, and planar CMOS electronics were larger in size and limited in adaptability with the human body. Unwillingly, such obsolete device creates localized heating, power-loss and grumpy data performances.
About
-By Valentina De Vincenti
Printed decal sensors, wearable wirelessly connected devices have widely change the approach to wellbeing and other countless applications. Despite they have been around for a while now, manufacturing such devices is still challenged in terms of performances and production costs, especially to integrate voluminous metal-oxide semiconductor (CMOS).
Unprecedentedly, a costless and reliable 3D high-speed printing fabrication process for CMOS full integration and packaging has been developed by Muhammad Mustafa Hussain and his team from the Integrated Nanotechnology Laboratory, under the Computer, Electrical and Mathematical Sciences and Engineering (CEMSE) Division.
"In the age of the Internet of Everything - IoE -, we need IoE applications to be data relevant, where sensors and actuators are fully integrated monolithically or heterogeneously with fast, low-power, and high-performance logic and radio-frequency (RF) devices," stated Hussain, Professor of Electronic Engineering (EE).
Attempts for 3D fabrication of decal electronics were previously made. But, rigid, bulky, and planar CMOS electronics were larger in size and limited in adaptability with the human body. Unwillingly, such obsolete device creates localized heating, power-loss and grumpy data performances.
In the move toward full integration, Hussain along with Galo Torres Sevilla, first author of the findings and a KAUST Ph.D. graduate, chose two lighter innovative solutions: zinc-oxide for memory devices (NAND and NOR), data processing (logic gates), and buffering (inverters); and aluminium for sensor connectivity (ring-oscillator).
The team's innovative fabrication process grounded on former CMOS manufacturing technology - photolithography and deposition, to blend thin-film based electronics on silicon (100) wafer. Then, with 3D printing decal electronics were interconnected with aluminum wires on soft substrates backed by an adhesive layer at 10 times faster speed.
Hussain and co-workers obtained a roll-to-roll (sensor to package) fabrication platform for sensors which can work on different applications. The 3D inject printing allows writing conductive wires on different substrates, such as clothing or papers varying in shapes and colors.
"With such newest technique, you can place an highly adaptable and reliable pressure-sensing decal on a tire to monitor it while driving and then peel it off and place it on your mattress to learn your sleeping patterns," said Sevilla reporting on successful stress tests run either on single components and on the whole system.
The great success of team's manufacturing process has been revealed already at its early stage. Further research will hype the potential of such adaptable and affordable technique opening up new frontiers in health monitoring as well as other printed communication devices and flexible high-performance electronics.