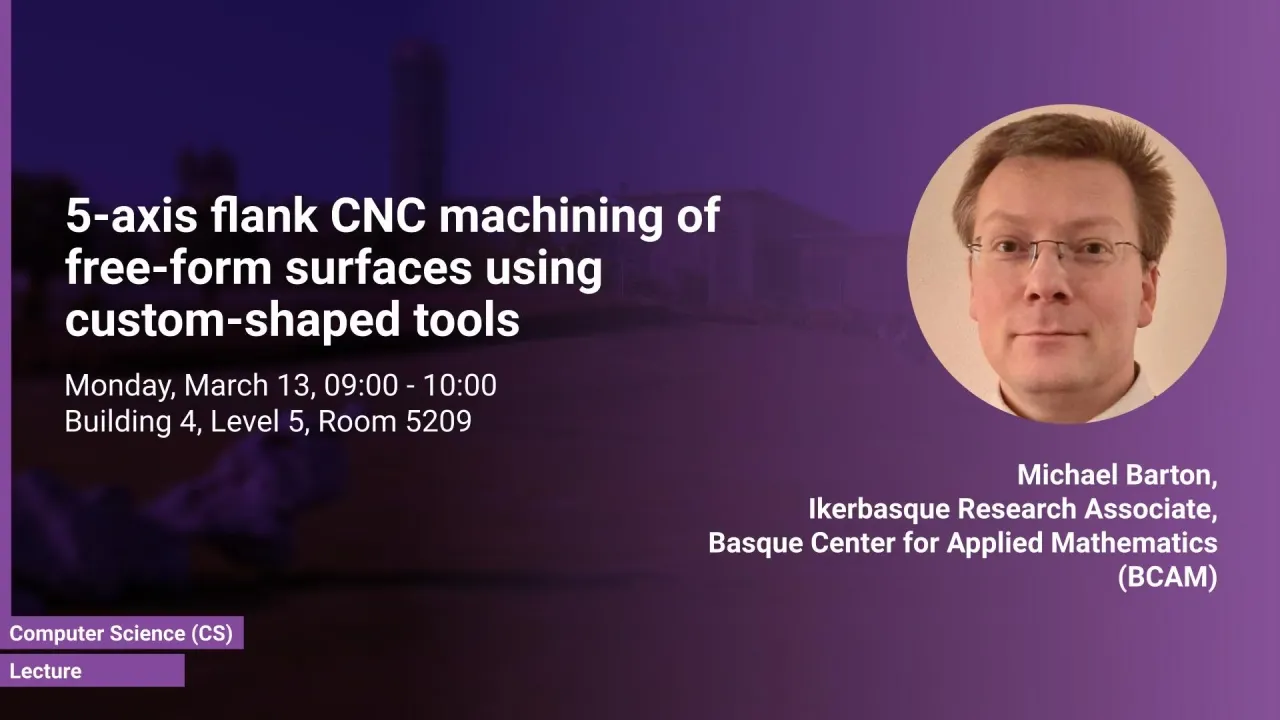
5-axis flank CNC machining of free-form surfaces using custom-shaped tools
In this talk, I will discuss our recent advances in approximation of free-form surfaces by motions of curvature varying tools in the context of 5-axis flank CNC machining. In particular, I will discuss path-planning strategies using fixed tools, or custom-shaped ones, and on an example of spiral bevel gears will demonstrate even more efficient variant of flank machining, called double-flank.
Overview
Abstract
Computer numerically controlled (CNC) machining is the leading subtractive manufacturing technology and even though it is in use since decades, it is far from being fully solved and still offers a rich source of challenging problems in geometric computing and motion planning. Flank, aka peripheral, machining is the finishing stage of the machining process where the tool touches tangentially a to-be-machined surface. The cutting tools used in this stage are typically conical or cylindrical, however, the majority of industrial benchmark geometries like blades or impellers are doubly curved which raises a question whether one shall not use curved tools for manufacturing of curved surfaces, instead of at ones.
In this talk, I will discuss our recent advances in approximation of free-form surfaces by motions of curvature varying tools in the context of 5-axis flank CNC machining. In particular, I will discuss path-planning strategies using fixed tools, or custom-shaped ones, and on an example of spiral bevel gears will demonstrate even more efficient variant of flank machining, called double-flank.
Brief Biography
Dr. Michael Barton is an Ikerbasque Research Associate and a co-leader of the Mathematical Design and Simulation group at the Basque Center for Applied Mathematics (BCAM). Prior joining BCAM, he was a post-doctoral fellow at JKU Linz (Austria), Technion (Israel), and King Abdullah University of Science and Technology – KAUST (Saudi Arabia). He published over 60 peer-reviewed research articles; h-index 20 (Scopus), 21 (Google Scholar). He received the Ramon & Cajal fellowship in 2016 and the Young Investigator Award from the Solid Modeling Association (SMA) in 2019. He serves as an associate editor in Computer-Aided Design (CAD, Elsevier), Graphical Models (GMOD, Elsevier), and Computer Graphics Forum (CGF, Wiley) and is a member of International Program Committees at several top conferences of geometric modeling and processing. Currently he is the coordinator of a €3M FET-OPEN 2018 project on Analysis, Design, And Manufacturing using Microstructures (ADAM2). Altogether, Dr. Barton received funding from national governments, EU, and industrial partners in the total amount of €1.24M. His research spans numerical analysis, geometric modeling and processing, particularly approximation of free-form (NURBS) objects.