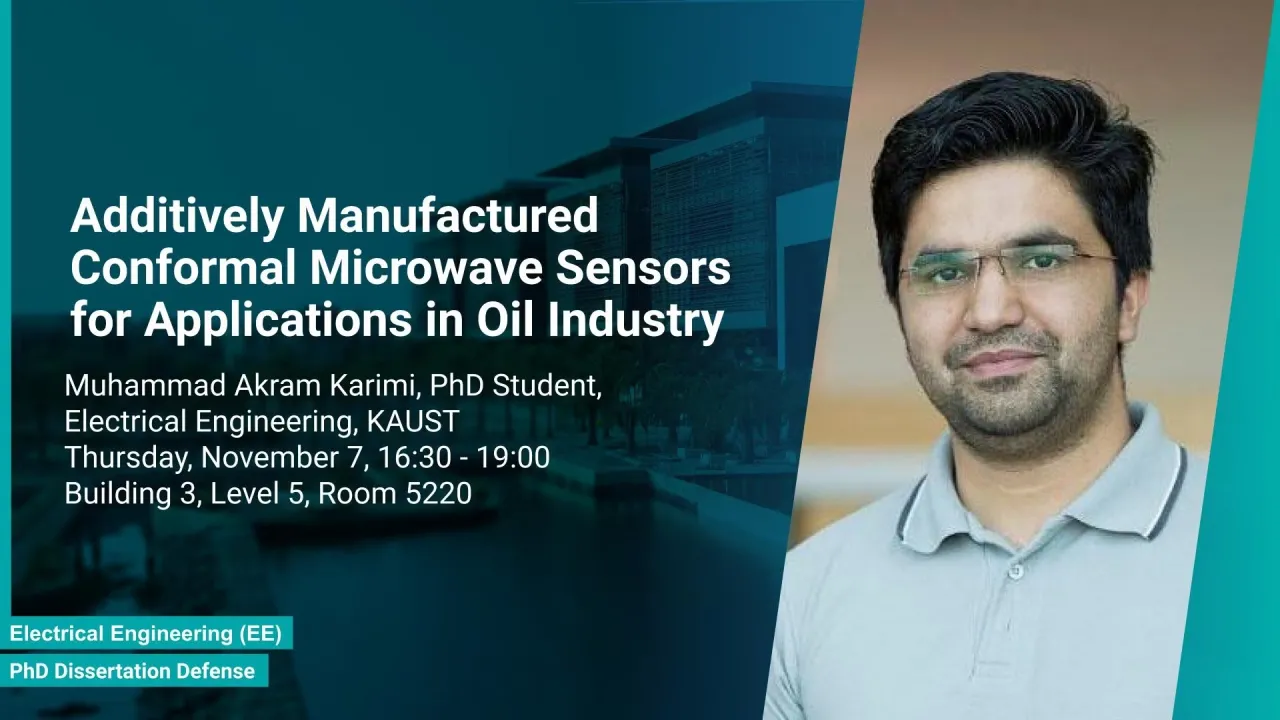
Additively Manufactured Conformal Microwave Sensors for Applications in Oil Industry
Modern industries are adapting smart ways of monitoring their processes to ensure smooth operations. Sensors capable of early detection of a problem are becoming the norm in industrial processes. This is key to the development of the “Internet of Things” (IoT), in which billions of interconnected devices will work together to make smart decisions. Sensors that can detect and communicate the process information are essential ingredients of any IoT-enabled network. Since billions of such sensor nodes will be required in the future, the low cost will be an important feature for these devices. Consistent with the above-mentioned trends, the oil industry is also adapting smart monitoring and actuation mechanisms for its day-to-day operations. This thesis is focused on developing low-cost sensors, which can increase oil production efficiency through real-time monitoring of oil wells and also help in the safe transport of oil products from the wells to the refineries.
Overview
Abstract
Modern industries are adapting smart ways of monitoring their processes to ensure smooth operations. Sensors capable of early detection of a problem are becoming the norm in industrial processes. This is key to the development of the “Internet of Things” (IoT), in which billions of interconnected devices will work together to make smart decisions. Sensors that can detect and communicate the process information are essential ingredients of any IoT-enabled network. Since billions of such sensor nodes will be required in the future, the low cost will be an important feature for these devices. Consistent with the above-mentioned trends, the oil industry is also adapting smart monitoring and actuation mechanisms for its day-to-day operations. This thesis is focused on developing low-cost sensors, which can increase oil production efficiency through real-time monitoring of oil wells and also help in the safe transport of oil products from the wells to the refineries.
Water is typically present underground in the vicinity of oil reservoirs. Water and steam are also pumped into wells to enhance the oil recovery rate. Water from these sources mixes with the oil, which complicates the oil recovery process. This unwanted water must be quantified accurately if it is to be handled and processed properly. The amount of water produced from a particular oil well also determines whether it is economically viable to continue to extract oil from that well. Moreover, an abrupt increase in the amount of water represents a malfunction of the well formation underground, which may lead to failure of the well. For the above-mentioned reasons, it is important for oil producers to be able to quantify the exact amount of water produced from a particular well in real-time. Sensors that can measure the water fraction in oil are known as water-cut (WC) sensors, and they play a significant role in the efficient and safe recovery of oil from a particular site. Typically, these sensors are placed outside an oil well to make placement, access and data recovery easier.
Non-intrusive WC sensors are preferred because intrusive sensors can cause undesirable pressure drops and also suffer from wear and tear effects that limit their service life. Moreover, a single sensor capable of sensing the full range of the water fraction (0–100%) is desired because the water fraction varies at different production sites at different times. Unfortunately, the WC sensors available at present are either intrusive, cannot cover the full WC range or require bulky flow conditioners before the sensing stage.
Microwave-based sensors can typically cover the full water-fraction range (0–100%), which is why they have a major market share of over 50%. However, existing microwave-based WC sensors are intrusive in nature. In this thesis, we demonstrate a pipe-conformable, non-intrusive microwave sensor that can cover the complete WC range independent of the pipe orientation. The sensor operates on dielectric measurement principles and comprises a microstrip T-resonator that has been optimized for a pipe surface. Orientation insensitivity has been achieved by utilizing two mutually orthogonal spiral-shaped modified T-resonators. The sensor has been realized through additive manufacturing techniques (a combination of 3D and screen printing), making it ultra-low-cost and lightweight. Testing of the sensor has been conducted in the global research center of Aramco in Houston, USA and in an industrial flow loop located in Bergen, Norway. The measured results are accurate to within 1–2% and have a resolution of 0.1%. Successful lab validation of the design has led to the development of an industrial prototype, which has now obtained hazardous area safety certification and is ready to be tested in the field.
Oil wells are typically drilled vertically, and the WC can be measured once the fluid mixture rises to the surface. Therefore, there is no need to place WC meters in the challenging downhole environment. However, modern wells have horizontal branches, which originate from the main vertical well in order to maximize the underground area. It is possible that water may find its way to one of these horizontal branches, which would increase the overall WC of fluid produced by that well. In this scenario, the WC meter placed at the top cannot identify the problem location downhole; the only thing the WC meter on the top can inform the operator about is the sudden increase in the WC. At present, production from such a well is stopped to allow manual identification of the problematic branch using robotic platforms. The ideal solution would be a dedicated WC meter for every downhole branch. However, the downhole environment is quite challenging due to high temperature, high pressure, and limited available space. Moreover, any WC meter installed downhole must be very robust because it cannot be serviced after installation.
Saudi Aramco is developing a new retrievable downhole system, which allows downhole equipment to be serviced every 3–5 years. Compatible with that system, this thesis proposes a compact version of the WC sensor for the downhole environment. In the downhole version, metallic housing has been used to function as a ground plane for the coaxially located spiral resonator. This housing also protects the sensor from environmental effects.
In addition to the efficient production of oil, its safe transport is also a concern for the industry. This is because oil leaks can be a major health and safety risk not only for humans but also for marine life. It is physically impossible to inspect a network of thousands of kilometers of pipelines manually. For this reason, the industry is moving towards finding automated solutions for reporting leaks. However, existing leakage detectors suffer from low sensitivity, high false-positive rates, and dependence on environmental effects. In this thesis, we propose to use microwave technology to overcome the above-mentioned challenges, particularly for pipe joints, which are vulnerable to leakage due to wear and tear effects. The leakage sensor has been designed to conform to the shape of the pipe joint. The unique design allows our leak detector to clamp on top of the existing pipe infrastructure. The sensor is extremely sensitive and can detect even minute leaks of less than 0.5 mL. By incorporating these smart pipe joints, leaks and their locations can be reported to the concerned authorities in an immediate and automated fashion.
Brief Biography
Muhammad Akram Karimi received his B.S. degree in electrical engineering from the University of Engineering and Technology (UET), Pakistan in 2013. He received his M.S. degree in 2015 from the Electrical Engineering department of King Abdullah University of Science and Technology (KAUST) where he is currently pursuing his Ph.D. degree. His research is focused on the flexible and conformable microwave sensors for industrial applications.