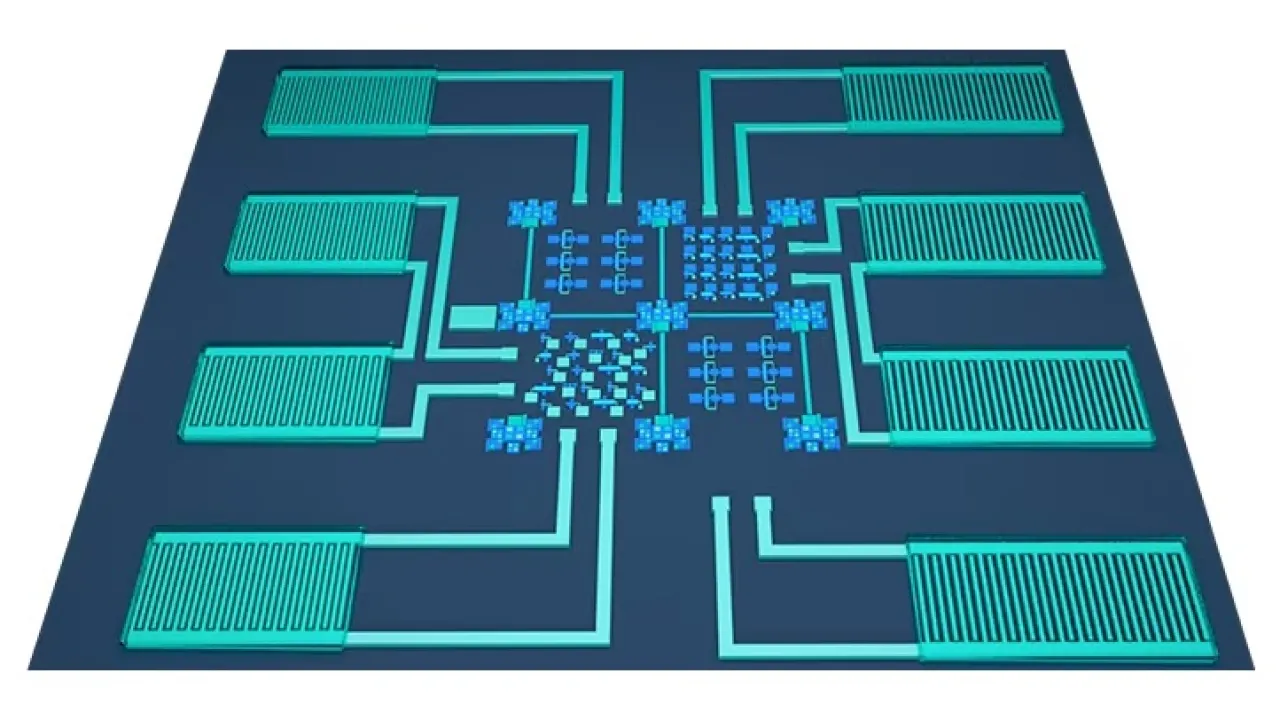
Single-electrode material streamlines functions into a tiny chip
Ruthenium oxide is used to integrate energy-storing microsupercapacitors and thin-film electronics at the transistor level.
About
The ability to combine many functions into a single microchip is a significant advance in the quest to perfect the tiny, self-powered sensors that will expand the Internet of things. KAUST researchers have managed to combine sensing, energy-harvesting, current-rectifying and energy-storage functions into a single microchip.
“Previously, researchers had to use bulky rectifiers that converted intermittent harvested electrical energy into steady direct current for storage in electrochemical microsupercapacitors,” says Mrinal K. Hota, research scientist at KAUST and lead author of the study.
Hota explains that the key to integrating everything into a single chip was the development of ruthenium oxide (RuO2) as the common electrode material connecting all devices in the microcircuits. The team envisages a broad range of applications from monitoring personal health indications directly from the human body to environmental and industrial sensing.
“Our achievement simplifies device fabrication and realizes significant miniaturization of self-powered sensor devices,” says project leader Husam Alshareef.
The ruthenium-oxide contacts are laid onto a glass or silicon substrate to connect sensing, energy-harvesting and current-rectifying electronics with one or more electrochemical microsupercapacitors that store the electrical energy. This creates a tiny system that can operate without any battery power. Instead it uses available body movement or machinery vibrations as the reliable and continual source of energy.
“Unlike a battery, electrochemical microsupercapacitors can last for hundreds of thousands of cycles rather than just a few thousand,” Hota points out. They can also deliver a significantly higher power output from a given volume.
A key to creating electrode material suitable for connecting all devices was to make optimal ruthenium-dioxide surfaces with controlled roughness, defects and conductivity. These features enabled the team to use RuO2 for both electronics and electrochemical microsupercapacitors.
Read the full article